Gas Metal Arc Welding (GMAW)—also known as Metal Inert Gas (MIG) welding or Metal Active Gas (MAG) welding—is a semi-automatic or automatic arc welding process in which a wire electrode and shielding gas are fed through a welding head.
The process is quite hostile to any camera in or around the welding process. As such, for a successful application of a Weld Camera for remote monitoring of GMAW, the camera needs to be designed to meet harsh environmental conditions—including high heat, extreme variations in arc light intensity, weld smoke, and metal spatter.
But that’s just the starting point. A Weld Camera must not only be industrially hardened to suit the tough environment conditions; it must produce weld images with enough clarity and detail to provide operators useful guidance for making in-process adjustments.
The GMAW welding process takes place by means of constantly supplying a consumable metal electrode in the form of a wire and shielding the arc with some sort of gas, as shown below.
(courtesy of substech.com)
GMAW Transfer Modes
The GMAW process has three transfer main modes—spray, short circuit, and globular.
Spray mode is where a stable electric arc passes metal from the electrode to the work piece. It’s a cleaner process than other modes and easier to image, as the arc has a fairly consistent intensity.
Globular transfer is the most undesirable mode as it generates high heat, poor weld quality, and plenty of spatter. In globular transfer, balls of molten metal build up on the end of the electrode and eventually drop on to the work piece, causing a large weld pool, uneven surfaces, and huge variations of arc brightness.
Short Circuit uses lower current than Globular, providing less heat input, but is a similar process, in which balls of molten metal form on the electrode and bridge the gap between the electrode and the work piece, causing a short circuit that extinguishes the arc, which is quickly reignited when the ball of molten metal disconnects from the electrode tip. The result is that the arc is constantly being short-circuited, extinguished and reignited causing extreme fluctuations in brightness.
Imaging the Wide Brightness Range of GMAW
In GMAW, achieving the necessary image quality can be a significant challenge. GMAW is the most common and readily available metal joining process—preferred for its versatility, speed and the relative ease of adapting the process to automation—but from an arc-monitoring point of view, it’s the most difficult welding process to monitor.
This difficulty arises because GMAW normally involves huge changes of brightness—ranging from an almost-dark scene between pulses of a weld arc to the full-on blasts of a short-circuited arc’s pulses of light, which last for variable durations and have a large range of brightness variation due to high-speed modulation.
While some welding processes may have an arc that appears constant to the human eye, the pulsing arcs in short circuit GMAW may appear vastly different in recorded videos, as most cameras acquire images at rates of 25-50 Hz. If the GMAW process is modulated at a similar speed, some images acquired could show a completely dark arc.
Adding to the complexity of GMAW remote monitoring, the GMAW process can vary significantly from one application to the next depending on the arc parameters (e.g., current value, type of modulation, pulse duration, and wire supply speed).
These remote monitoring challenges contribute to two prevalent quality problems in GMAW: dross (solid impurities in the weld) and porosity (air pockets or voids formed in the weld material as it solidifies), both of which lead to poor-quality welds.
Fortunately for welding manufacturers, these quality issues can be overcome with better monitoring. Using a Weld Camera with High Dynamic Range imaging capability can produce images with enough clarity to:
- Detect the presence of dross in the weld pool that could lead to poor welds after cooling.
- Identify porosity in the weld bead that could reveal a potential for reduced weld strength.
- Confirm that the surface of the molten pool and the immediate surrounding parent metal is kept clean of impurities.
- Verify alignment of the weld head and filler material to the seam.
- Monitor the smoke to determine if any changes to the welding metallurgy or shielding gas are occurring.
- Confirm the size and shape of the shielding gas to ensure correct placement around the arc to isolate the weld from ambient contamination.
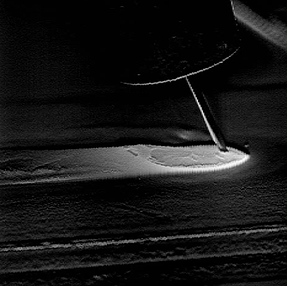
MIG Weld Image
Conclusion
GMAW presents remote imaging challenges—wide brightness variations, harsh camera conditions, varied processes—that require a Weld Camera with sufficient dynamic range to produce high-quality images, versatility for use in multiple types of GMAW, and a design that can withstand the welding environment.