Welding of thick-walled steel pipe or flat plate greater than about 35-40 mm (approx. 1.5”) is typically done by Submerged Arc welding (SAW) processes. Typically, this includes welding of pipe material for oil and gas or power generation, wind turbine structures or sub-assemblies used in construction.
Sub-arc welding (courtesy of Miller)
Sub-arc welding is used for these processes because of the large amount of weldment material required to complete the joining process. Normally in such welding processes, a V-groove edge preparation is used, which, when assembled, creates a sizable gap that needs to be filled with weldment to complete the gap. This is done by making multiple passes of a SAW process until the V groove is completely filled.
SAW has the advantage that it uses flux to cover the weld arc, so there is minimal spatter, making it safer for operators, leading to high travel speeds, high quality and better productivity. However, because so many passes of a SAW process are needed, huge amounts of power and heat are introduced into the parent material inevitably causing distortion, requiring complex straightening work post welding. In addition, because of the number of SAW passes needed, there is large consumption of welding wire used in the process.
Multi-Pass Welded Joint (courtesy ResearchGate.net)
Contrast that to Laser Beam Welding (LBW) or Electron Beam Welding (EBW) processes, which provide focused, high-energy beams that can penetrate deep into a material with low aspect ratios, saving welding time and consumption of wire. Such processes, however, have very small beam size, so they require very precise weld seam preparation in order to avoid gaps in the welding process.
Laser Beam Welding (courtesy ME Mechanical)
A recent solution to the above drawbacks of the individual processes is Hybrid Laser Arc Welding (HLAW), where a laser beam and an arc process such as SAW act simultaneously on one welding zone. The hybrid approach minimizes the volume of weld wire needed to complete the weld process and related heat input and material distortion, while reducing the amount of edge preparation of the material required, resulting in a process that is able to meet the quality requirements demanded by the application.
Hybrid Laser Submerged Arc Welding Principle (courtesy sciencedirect.com)
Because it is so difficult to monitor both processes simultaneously, it is almost essential to add weld cameras to the process to be able to monitor each process separately. This requires special weld camera hardware to be able to see the details of each process.
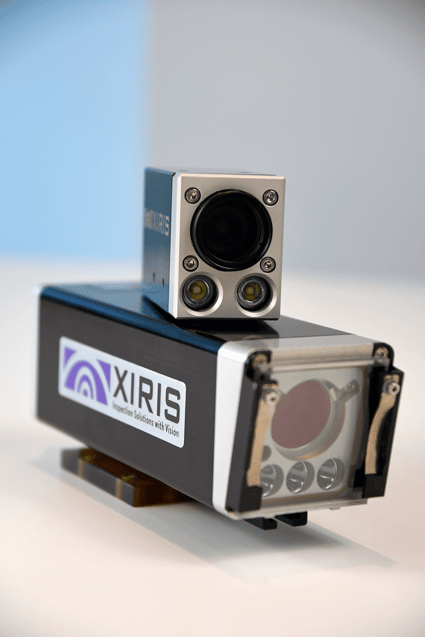
For a laser beam welding process, an open arc weld camera can be used to look either coaxially through the laser beam delivery system, or off axis to look at the laser spot at an oblique angle. Either way, the camera needs to be able to see a huge range of light generated by the laser spot while also being able to see the darker surrounding material. For the SAW process, a weld camera dedicated to seeing the alignment, stick-out and flux presence is needed. Such a camera must be sensitive to low light levels while providing graphical aids that allow operators to properly monitor the process.
Xiris has developed a Hybrid camera system that incorporates the XVC-1000 Weld Camera for monitoring the laser welding process and the new XVC-S100 Weld Camera for monitoring SAW. The output of both cameras can be presented on to a single computer screen using WeldStudio™ 3 software, allowing operators to see the detail of both processes at the same time. Features such as torch to seam alignment of both processes, laser spot size and shape, wire feed rates and melt pool geometry can all be tracked easily with such as set up, driving welding quality and productivity.
To learn more about Xiris’ weld monitoring cameras, visit www.xiris.com/weld-monitoring-cameras or speak with one of our knowledgeable product experts.
Stay up to date by following us on social media or subscribe to our blog!