Being able to detect welding discontinuities to classify and correct any defects during a welding process is critical to produce reliable and quality welds. As experts in weld camera monitoring solutions with both visual and audio components, we at Xiris have identified how several welding discontinuities leading to defects can be spotted using Xiris weld cameras and weld microphones.
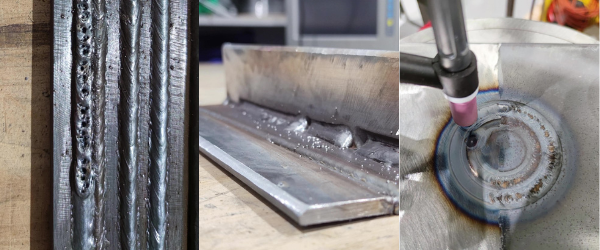
It is important to note that not all weld discontinuities are defects. A discontinuity can be defined as a lack of continuity or cohesion; an intentional or unintentional interruption in the physical structure or configuration of a material or component. A discontinuity, however, may not cause rejection if it is under permissible limits stated in code or standards. Comparatively, a defect is one or more discontinuities whose aggregate size, shape, orientation, location, or properties exceed any stated limits, therefore not meeting specified acceptance criteria that may be subject to rejection.
Recently our experts held a webinar where they walked through a few discontinuities leading to defects and how they can be identified using a Xiris weld camera along with the Xiris WeldMic™.
Test Your Knowledge #1:First, put your weld defect knowledge to the test. What defect can be seen in this video?
|
Porosity
As voted by our audience, porosity is one of the most common defects found in welding processes.
Porosity is the presence of pores or cavities on the surface of the weld bead which as seen in this case, results from unwanted atmospheric gases contaminating the weld pool due to insufficient shielding gas causing a significant lack of coverage.
Using the weld camera and weld microphone, porosity can be identified by the large noticeable pores on the surface or the change in the weld sound that may be more obvious to those with much welding experience.
Have a look for yourself in the video above.
Lack of Fusion
Another common weld defect is lack of fusion. Lack of fusion can occur in one of two ways; (1) lack of root fusion where the first weld bead does not fully fuse with the parent material or (2) lack of sidewall fusion where the weld bead deposited immediately next to the parent plate fails to fully fuse. Lack of fusion can often occur in a welded joint and can be caused by several reasons, including an inconsistent wire feed as seen in this video example.
In this case, there was inconsistent arc length due to insufficient wire feed. Using the weld camera and microphone, the defect can be identified by the noticeable pauses in the weld sound or the irregularity and craters in the weld bead that can be seen. From another camera angle, large globular droplets can be picked up which are another symptom of the issue and can help in identifying this defect.
Take a look in the video above.
Test Your Knowledge #2:Here is another quiz to test your weld defect knowledge. What defect can be seen in this video?
|
Burn Through
Another defect that our experts discussed and the final one we will mention in this blog (download the full webinar recording to learn more) is burn through. Burn through is when the weld penetrates deep and reaches the weld root, essentially melting through the entire thickness of the base metal. This of course is more common on thinner workpieces or material with low thermal conductivity. Like most defects, burn through can severely decrease the integrity of a welded joint as any gaps and holes become stress points that are likely to crack under a load.
Caused by excessive heat input, this video example of burn through showcases how a weld camera can visually pick up the holes in the weld, but also the changes in sound that the tube cavity makes when burnt through.
Take a listen in the video above.
Test Your Knowledge #3:Here is the final quiz to test your weld defect knowledge. What defect can be seen in this video?
|
A Xiris Weld Camera and weld microphone can help in identifying discontinuities leading to defects during the weld process. Using both visual and audio components, the powerful tools can pick up indicators of a serious issue that may need to be addressed. Early action in identifying and correcting any discontinuities or defects will help improve overall quality and reduce scrap.
Download your own copy of the full webinar to learn more about Welding Defect Detection Using Vision and Audio.
Stay up to date by following us on social media or subscribe to our blog!