Xiris Weld Cameras are often used to enable operators to view the welding process remotely and monitor welding processes, improving operator safety and efficiency. With the need for higher levels of efficiency and automation, adding weld cameras that can be used to measure and track welding features is becoming ever more important.
The XVC-750 weld camera combines 140+dB of High Dynamic Range (HDR) capability with Near Infrared (NIR) sensitivity to provide high contrast images in and around the melt pool.
NIR sensitivity enhances the image contrast in the image by adding a component of the heat present in a weld environment to the visible light present.
(Hold on! Keep scrolling to check out the images!)
The result is a higher contrast image especially for features with high heat emission such as the melt pool and weld bead but also for other features in the vicinity of the weld that reflect the heat such as the parent material, weld seam of added welding wired.
The enhanced contrast generates an image where the features of an open arc weld process can be more clearly seen and detected by human operators or machine vision processes alike.
See Fig 1 below for an image example of a weld process taken by an XVC-750 camera.
Some of the Key Benefits of the XVC-750 camera system are:
- Excellent high contrast images for Machine vision tasks, particularly for monitoring the melt pool and cooling bead;
- A clear view of all the important features in and around the melt pool and welding process.
- High-resolution imaging to detect possible defects in the melt pool and cooling bead.
- Based on the same versatile compact camera platform as other XVC700 cameras that allow for the optics to be mounted at various angles to the main camera body.
The better contrast XVC-750 images that allow for better process monitoring by the operators are also better for automated Machine Vision tasks. When coupled with Xiris’ WeldStudio Pro software, machine vision analysis is much more robust because of the improvement in contrast of the NIR images.
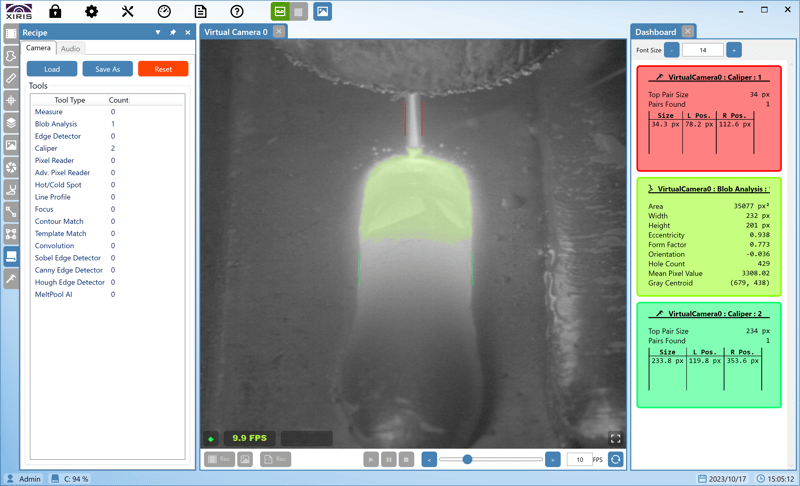
Figure 2 shows Machine vision tools in WeldStudio Pro with measurements for wire location and weld bead width measurement occurring in real time using the caliper tool. Also in the above image, the MeltPool-AI tool is shown highlighting the melt pool and performing precise melt pool shape and size measurements, including:
Area
|
Hole Count |
Width |
Perimeter
|
Height | Euler Number |
Eccentricity | Mean Pixel Values |
Form Factor | Centroid |
Orientation |
And many others. These measurements can then be used for automated process monitoring and possible process adjustments.
The enhanced images provided by the XVC-750 helps in the detection of discontinuities and possible defects that are difficult to detect otherwise, including wire feeding issues, burn-through, contamination, porosity and lack of fusion or off-seam.
The detection of these can be especially effective when using Artificial intelligence (AI) or Machine Learning (ML) defect detection methods.
![]() |
![]() Figure 4 – GMAW -Fillet Joint Lack of Fusion
|
The NIR capability of the XVC-750 enhances image contrast in most cases of weld processes. For some applications however, it may be beneficial to add additional illumination to see more of the background around the weld, such as the base material, more clearly.
This is especially true if the weld arc and bead is small relative to the entire Field of View (FOV) when the camera is used in trailing view applications; or when trying to see the seam more clearly and its alignment to the torch for leading view applications.
See Figure 5 for an example of a leading view application.
Because of its compact size and the variety of optics angles in which it can be configured, the XVC 750 weld camera is ideal for automated, and robotic welding systems. But The XVC7x0 series :
In summary, the XVC-750 weld camera is a great camera choice for most production welding applications. It can be used to improve the contrast of certain open arc welding processes for operator monitoring, allowing the operator to view the process remotely.
Also, because it generates higher contrast, stable image, the XVC-750 camera can be used in applications where machine vision analysis is required to extract measurements of various features of the weld, making it suitable for integration into all types of automated welding systems.