A major challenge in producing good quality pipe on a welded Pipe Mill is the build-up of slag on the ferrite bundle used inside the pipe. Slag is a mixture of metal oxides and silicon dioxide that is a byproduct of separating the steel from its raw ore. Ferrite bundles are typically placed inside the pipe to help concentrate the electrical radiation towards the seam to be welded. During welding, slag can drip down from the molten metal at the edges of parent material, building up deposits on the ferrite bundle casing surface inside the pipe. The result is a potential reduction in power concentration at the weld point, which could lead to weakened pipe welds. Known as a “Ferrite breakdown”, it needs to be identified early in the weld process in order to avoid poor welds from making their way down the line or out the door to the customer.
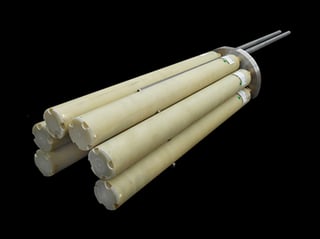
(courtesy www.piecsa.mx)
One obvious solution would be to periodically stop the mill and open up the pipe and visually inspect the casing; this of course is not always a feasible or desirable solution. A better approach to identify changes over time is by monitoring the shape of the weld bead. This can be done by operators who might visually inspect the scarf coming off the tube for signs of change and or abnormalities. However, as slag could build up on the surface of the ferrite bundle casing which is inside the welded pipe, it is difficult for the operator to notice any slag buildup.
A better solution would be to use a laser based profile measurement system such as the Xiris WI3000. By using a precise laser with a high speed camera, multiple images of the weld bead and its immediate area can be taken. The shape of the weld bead can then be automatically analyzed for potential defects.
If there is slag buildup on the surface of the ferrite casing and less power makes it to the seam of the pipe, the top of the weld bead may become flatter or even concave as a result of reduced weld power concentration. Visually it may appear to the operator as a “pasty” weld and we like to call it a “freeze line” defect.
When monitoring the weld bead using a laser profile of the weld zone complemented with some real time geometrical measurements, the operator can be alerted to the freeze-line condition defect much sooner. As seen in the picture below taken from the screen of a WI3000, the operator is provided with a magnified view of the weld zone readily visible from afar. In this view the weld bead is starting to flatten and if it becomes concave, the operator would be alerted before a potential faulty weld is generated.
Screenshot from the Xiris WI3000 Laser Inspection System
The shape of the weld bead on an ERW pipe mill can provide much information. In particular, if a laser based profile measurement tool is used, such as the WI3000 from Xiris, early detection of defects such as freeze line can be made. Such defects often occur as a result of a reduction of power making its way to the weld zone resulting in incomplete heating of the weld bead. By providing early warning of such defects, operators can correct the problem before it becomes a critical failure.
For more information on how WI3000 can help reduce ferrite breakdown in your tube mill, visit Xiris.com