Over the past couple of months, we have discussed the number of challenges to the detection of defects during the deposition process in metal additive manufacturing (MAM), and how Short-Wave InfraRed (SWIR) thermal camera technology can address them. We first discussed the ability to obtain a better image despite any particulates from smoke and fumes in a harsh environment. In the second blog to the series, we discussed the considerable number of interrelated process parameters that need to be precisely controlled to produce parts that are destined for industries such as aerospace and healthcare, and the SWIR capability to achieve reliable measurements. We then moved on to discuss eliminating emissivity challenges with SWIR technology’s lower sensitivity to emissivity changes of a metal and as a result, increased accuracy. Most recently in the series, we highlighted how SWIR imaging can eliminate high contrast scenes and provide human-like vision.
In this blog, we are going to discuss the especially important topic which is at the core of Xiris and our products: increased safety for the operators of the equipment.
One of the challenges that arises in working with the metal additive manufacturing processes has to do with the presence of powerful lasers used in the metal melting process. The power and intensity of these lasers can be very harmful to the human eye and other tissue. As a result, any human error or ineffective operator training can lead to serious safety problems for the operator.
Using the Xiris XIR-1800 Thermal Camera with combined SWIR and HDR technology, operators can monitor the process at a safe distance, minimizing the chance of any workplace injury. Since SWIR imaging technology is able to see light in wavelengths of about 900 - 1700 nm, “eye safe” lasers that have a wavelength greater than approximately 1400 nm can be seen by SWIR imaging cameras like the XIR-1800. As a result, powerful laser sources in that wavelength can be used as illumination aids for imaging the metal AM process, and key defects that were not easily visible using other techniques can be better detected and measured without the need for extra protection or enclosures for the laser illumination. Such defects as seam presence, seam alignment, melt pool or weld bead geometry can be detected. This results in not only a more efficient, but a safer work environment for the operator, with no need to worry about the damaging of eye vision.
To learn more about the Xiris XIR-1800 Thermal Camera, you can request a copy of our most recent webinar on Thermal Analysis for Welding and Additive Research. In this webinar, our experts discussed how the XIR-1800 can open entirely new avenues of process development and research, from weld pool segmentation to metallurgical analysis. We also answer some frequently asked questions such as
- Can the XIR-1800 be used in high-speed laser cladding applications?
- Does the camera have good experience monitoring WAAM?
- How does the camera stay protected from vapor and dust in the monitoring process?
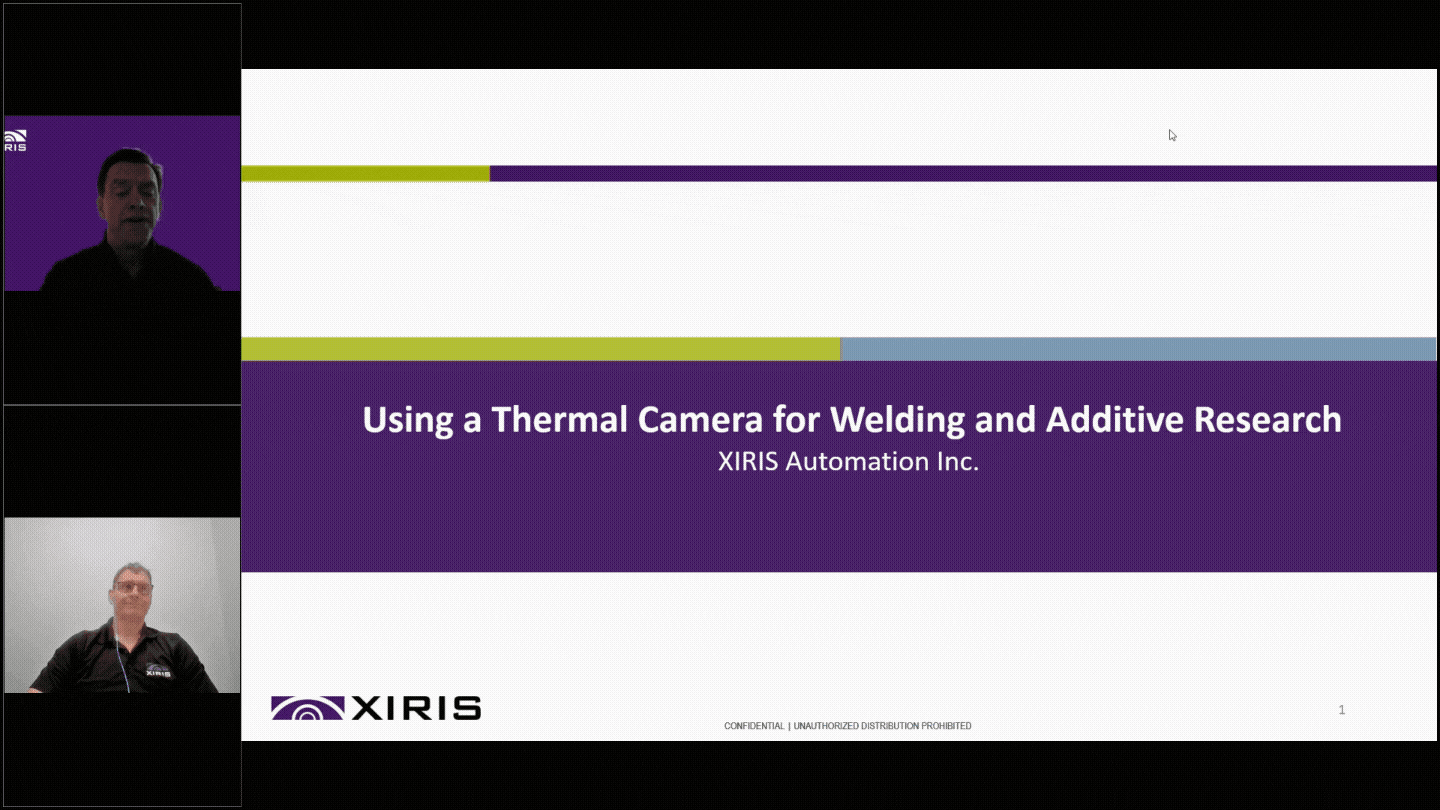
If you have any questions after reading this blog or watching the webinar, speak with one of our experts and have your questions answered one on one!
Stay up to date by following us on social media or subscribe to our blog!